Last time we explained how Alps Alpine uses magnetic sensors as encoders.
Here we explain the use of magnetic sensors as angle sensors.
Operating Principle of a Magnetic Angle Sensor
The basic operating principle is the same as for our magnetic sensor encoders in that changes in magnetic fields are converted into electrical resistance. That is then converted into voltage to become analog output.
Output of a Magnetic Angle Sensor
Alps Alpine's magnetic angle sensors contain four MR sensor elements inside the one package. Those four sensor elements deliver output in the form of two-phase signals with 90deg phase difference. These become the four signals +sin, -sin, +cos and -cos.
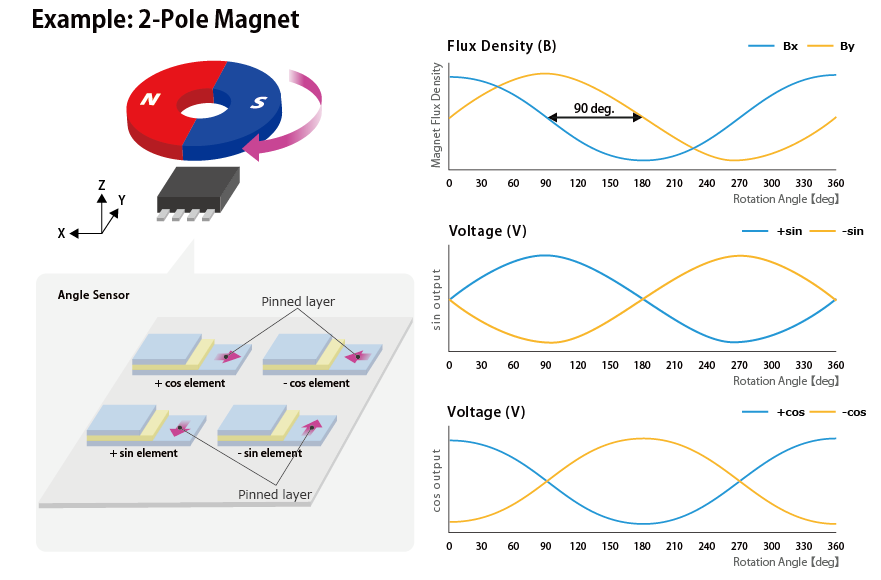
The four signals delivered as output by the sensor above (+sin, -sin, +cos and -cos) are amplified as required by the equipment it is incorporated into. Use of sin/cos computations means signals are dependent only on the angle of the magnetic field and are not affected by the strength of the magnetic field. Absolute angle is then computed on the customer's equipment side using an arctan (sin/cos) calculation.
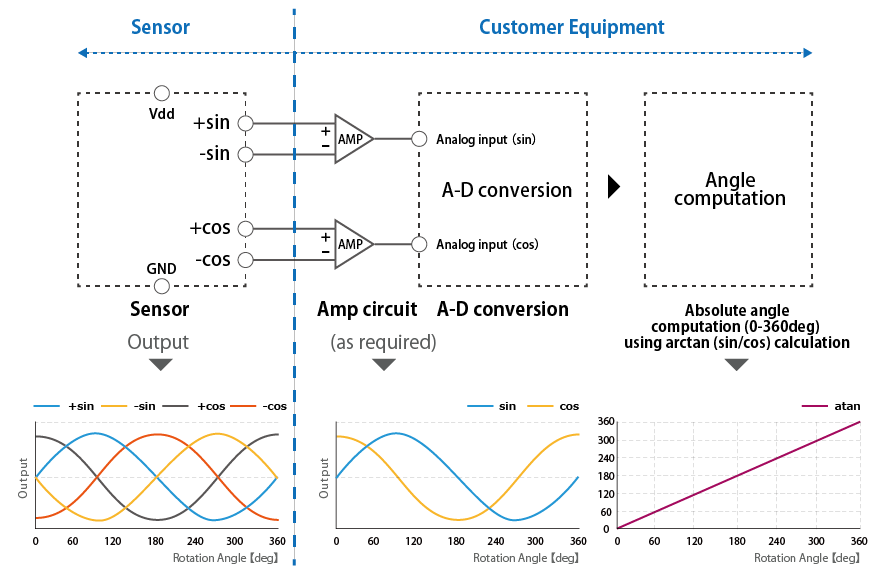
Features of Alps Alpine Magnetic Angle Sensors
Flexible Layout
Alps Alpine's magnetic angle sensors are like our magnetic sensor encoders in that sensor layout is highly flexible, allowing for greater design freedom. This makes it easy to include multiple sensors so that if one sensor happens to stop working, another will work, ensuring better reliability.

High-Efficiency/High-Precision Control
Using Hall sensors (encoders), normally three sensors are required for an angle sensor, but Alps Alpine's magnetic sensors make it possible to detect a linear rotation angle with a single sensor, helping to realize high-efficiency, high-precision motor control.
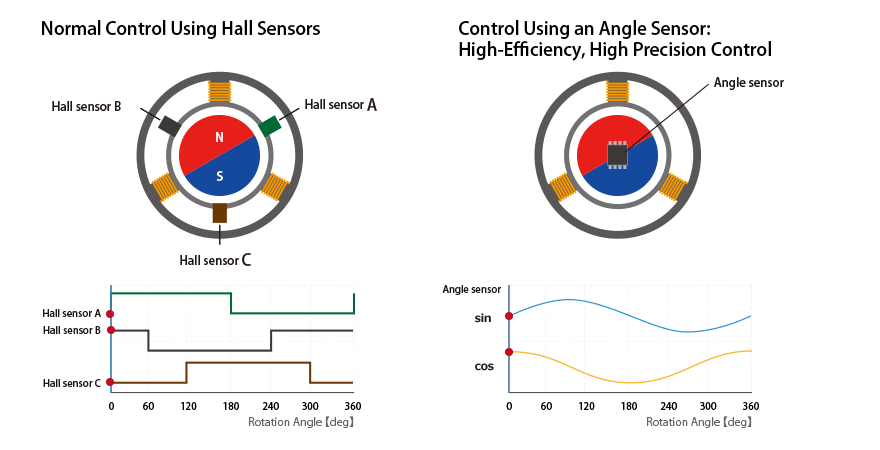
Over three installments we have introduced Alps Alpine's application of magnetic sensors to magnetic switches, encoders and angle sensors.
We also have a variety of other sensors, too, besides magnetic sensors.